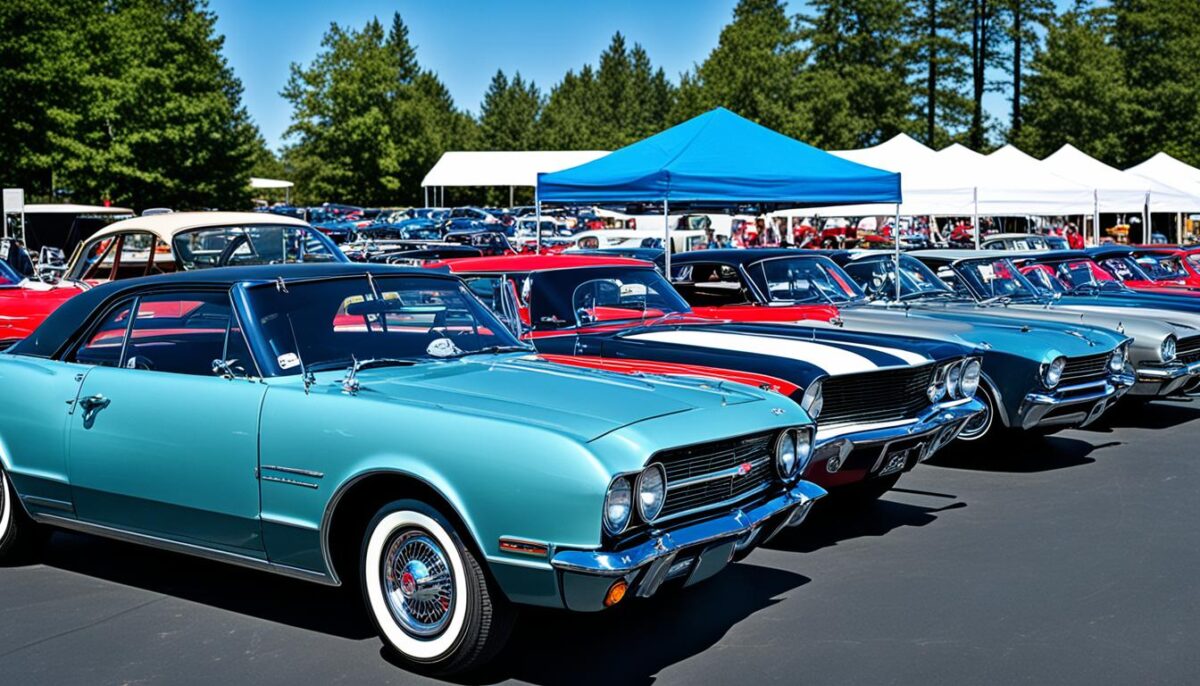
Discover, Learn, and Grow
Legal Business World is your premier destination for insights and knowledge about the car auction industry. We are dedicated to exploring the business of car auctions, innovative auction techniques, and the continuous development of the auction profession.
Our platform offers a wealth of resources tailored to meet the needs of auction professionals at every stage of their careers. From cutting-edge industry trends to practical advice on managing your auction house, Car Auction World is your go-to source for all things car auctions.
Why Legal Business World?
- Global Insights: Stay ahead with the latest news and trends from the global car auction market.
- Expert Perspectives: Gain valuable knowledge from industry leaders and experts.
- Innovative Solutions: Discover new ways to conduct auctions and enhance buyer engagement.
- Professional Development: Access resources and guidance to support your career growth and development.

Our Commitment
We believe in the power of shared knowledge and the importance of equal access to information. That’s why all our content is freely available, ensuring that every auction professional, regardless of their location or resources, can benefit from our platform. By participating in an auto auction, professionals can gain practical insights and experience, further enhancing their expertise in the field.
Featured Content
- Industry Trends: Explore the latest developments shaping the future of car auctions.
- Business of Auctions: Learn strategies for managing and growing a successful auction house.
- Auction Techniques: Discover innovative approaches to conducting auctions.
- Professional Growth: Access resources to help you advance your career.